Chivas Brothers makes heat recovery tech ‘open source’ to accelerate whisky industry’s net-zero journey
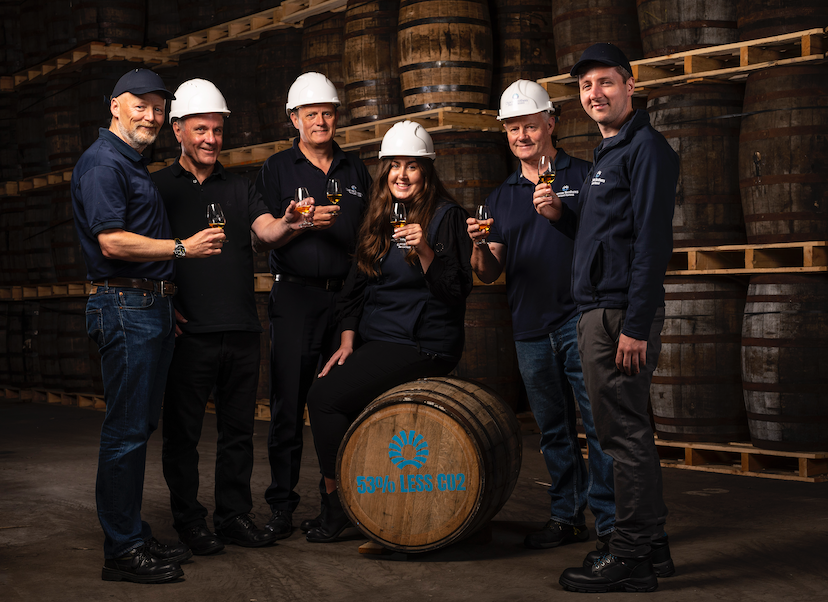
Pictured (L-R) Chivas Brothers' engineering team at its Glentauchers distillery – comprising Neil Fraser, engineering manager; Ewen Fraser, project manager; Trevor Buckley, distillery operations manager; Anna Pilkington, assistant project engineer; Fenton Perrie, project engineer; Darren Main, control engineer. (Credit: John Paul Photography / Chivas Brothers)
In a bid to expedite the whisky industry’s progress towards net-zero emissions, Chivas Brothers has made its pioneering heat recovery technologies open source.
The Scotch whisky business, a division of Pernod Ricard, owner of brands including Chivas Regal and The Glenlivet, makes the move on the back of significant carbon emissions reduction observed at its Glentauchers site in Speyside due to the application of these technologies.
The technologies, Mechanical Vapour Recompression (MVR) and Thermo Vapour Recompression (TVR), capture and recycle heat generated during the distillation process that would otherwise be wasted. This has led to a 48% reduction in total energy consumption at the Glentauchers distillery, translating into a 53% decrease in the site’s carbon emissions, an energy saving equivalent to powering 4,979 average UK homes for an entire year.
The Scotch whisky company aims to achieve carbon-neutral distillation by the end of 2026 and anticipates that the use of these technologies will reduce its overall energy consumption and carbon emissions by a third, equivalent to over 30,000 tonnes of CO2 annually.
The wider application of these technologies across the industry’s malt distilleries could result in annual savings of 1,756Gwh, enough to power 605,000 homes for a year, more than the combined total of Edinburgh and Aberdeen. However, these technologies may not be suitable for every distillery, the company noted.
Jean-Etienne Gourgues, chairman and CEO of Chivas Brothers, said: “Heat recovery forms a critical part of our commitment to achieve carbon neutral distillation by 2026. Findings with such significant impact must be shared; this technology has the potential to transform our industry and accelerate its progress to net zero.
“That’s why today we’re making our design process and implementation learnings available to all”, he continued. “As a business with a long history of innovation, we believe this is the right thing to do.
“Collaboration across our industry will be fundamental if we are to meet collective ambitions around sustainability, safeguarding the long-term future of our product and our planet. Understandably, this technology won’t be right for every distillery, but we encourage our peers to explore whether it has the potential to reduce their own carbon output.”
Chivas Brothers will host open house events at its Glentauchers site to showcase the technologies and facilitate industry learning. It is also publishing a case study highlighting the benefits and savings achieved through the application of these technologies. This initiative builds on the company’s 2021 pilot programme, partly funded by the Scottish Government through the Scottish Industrial Energy Transformation Fund, which achieved an 88% energy reduction.
Scottish Government Energy Minister, Gillian Martin, said: “Chivas Brothers has led the way with an innovative approach which has halved energy consumption at their Glentauchers distillery. Sharing this breakthrough with the wider whisky industry has the potential to advance efforts to reach net zero across the sector.
“Recycling heat from malt that would be the equivalent of powering all the homes in Edinburgh and Aberdeen could be a game changer for the industry, and a boost to Scotland’s economic growth while helping reach our climate change goals.”
Piller Blowers & Compressors GmbH, the company’s supplier, played an integral role in the programme’s success, as its technology was adapted for distillery applications. The technology demonstrated a Co-efficient of Performance of 12, meaning for every 1kwh of electricity input, 12 units of heat were generated.